Know these abbreviations when working with automation and robots
Do you have a grasp of the concepts when working with automation? And what does Industry 4.0 mean? This article gathers the most commonly used concepts and their abbreviations and gives you an insight into what the industry itself calls the new industrial revolution.
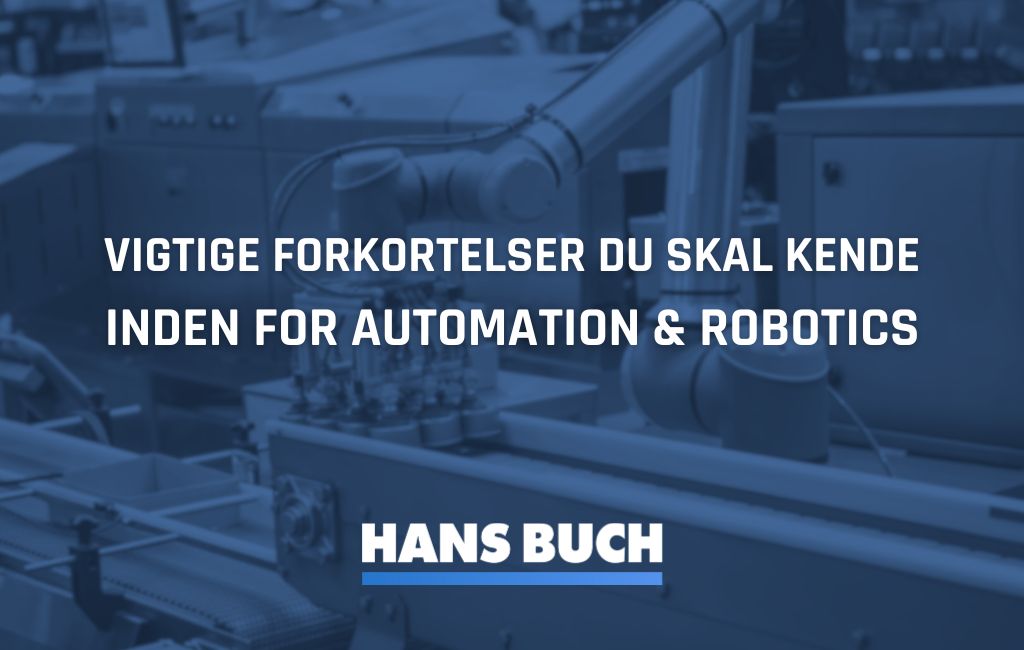
The broad industry is rapidly increasing automation in their processes and operations. The Automation & Robotics sector is experiencing a steep growth curve in both interest, development, revenue, and the influx of workforce directly or indirectly involved with automation.
Hardware or software? Automation requires both
Automatic controls, monitoring, and data collection place high demands on the technical components that the industry needs in terms of hardware when automated applications move in and take over parts of the process. It also demands reliable, secure, and user-friendly software that ensures the applications work appropriately.
Both hardware and software are therefore essential to consider when increasing automation, and the solutions generate many concepts, which you can read more about below.
Glossary: Here are the most common abbreviations in Automation & Robotics
The concept of Industry 4.0 has given the broad industry a range of new concepts worth noting when working with modern industrialization, characterized by a significant increase in automated processes of both hardware and software.
Within Automation & Robotics, there are several English terms that are often widespread with abbreviations and frequently used in both technical documents and everyday speech.
- PLC (Programmable Logic Controller): A digital computer used for automatic control of machines and processes in the industry. PLCs are central components in many automated systems.
- SCADA (Supervisory Control and Data Acquisition): A system that monitors and controls industrial processes remotely. SCADA systems collect data from various sensors and devices and allow operators to monitor and control processes.
- HMI (Human-Machine Interface): A user interface that allows operators to interact with machines and automation systems. HMIs display data and controls that enable the management and monitoring of systems.
- DCS (Distributed Control System): A control system distributed over multiple components or areas in an industrial process. DCSs are used to manage complex processes that require continuous monitoring and control.
- IIoT (Industrial Internet of Things): The application of IoT technology (Internet of Things) in industrial environments. IIoT connects machines, sensors, and systems so that data can be collected and analyzed to optimize production processes.
- AGV (Automated Guided Vehicle): A self-driving vehicle used to transport materials or products around a factory or warehouse. AGVs are automatically controlled using various technologies such as lasers, magnetic strips, or GPS.
- AMR (Autonomous Mobile Robot): Similar to AGVs but more advanced. AMRs use artificial intelligence and complex sensors to navigate independently in dynamic environments, where they can avoid obstacles and adjust their routes.
- CNC (Computer Numerical Control): A technology used to automate the control of machines via computer programs. CNC machines are commonly used in production for precise material processing.
- ROBOT (Reprogrammable, Multifunctional Manipulator): The term robot in this context often refers to a machine that can be programmed to perform a variety of tasks within automation and production.
- AI (Artificial Intelligence): The application of artificial intelligence to enhance the ability of robots and automation systems to learn, adapt, and perform complex tasks without human intervention.
- ML (Machine Learning): A sub-discipline of AI, where systems are trained to recognize patterns and make decisions based on data, which is widely used in advanced automation and robotics technology.
- ROS (Robot Operating System): A flexible framework for developing robot software. ROS provides tools and libraries that help developers design complex robot applications.
- MES (Manufacturing Execution System): A system that tracks and documents production in real-time. MES is used to optimize production processes by providing insights into production data and control options.
- CPS (Cyber-Physical System): Integration of physical processes with computer networks and software, often used in smart factories and advanced automation systems.
Perspective: Industry 4.0 – what does it mean?
Behind the abbreviations lie a range of concepts that are largely considered together when Industry 4.0 is mentioned. Industry 4.0 is a term that covers the so-called 4th Industrial Revolution. It is often abbreviated as “4IR” and is described as a rethinking of production and logistics processes and how they fundamentally function. It opens up new business models in the broad industry.
The core of Industry 4.0 is thus the integration of automated solutions with a focus on increased flexibility, adaptability, and efficiency, resulting in increased productivity and precision. It follows, in a way, the third revolution as a more advanced version, opening up new ways for value creation, waste reduction, enhanced quality, uniformity, and faster deliveries of larger volumes.
How the four industrial revolutions are divided
Each revolution describes an industrial era where technologies and raw materials have found their way into large-scale production of goods to such an extent that their integration into the industry has had a decisive impact on our society as a whole. The technological advancements are marked in four industrial revolutions:
The first industrial revolution:
The first revolution (1700-1800s) was about the transition from manual production to machine production using water and steam power. The textile industry was among the first to benefit from new technologies such as weaving machines and steam-powered engines. This significantly increased productivity and created new industries.
The second industrial revolution:
In the late 1800s to the early 1900s, there was a massive development in mass production and electrification. The use of electrical energy made it possible to create efficient production lines, such as the assembly line introduced by Ford. Steel production, the chemical industry, and railways, among others, took technological leaps during this period.
The third industrial revolution:
The 1960s to the 1990s characterize the third revolution, which was largely marked by the implementation of digital technology and automation. Electronics, computer technology, and programmable machines (such as PLCs) revolutionized the industry by enabling automated processes and data-driven production. Microprocessors and robots played a central role during this period.
The fourth industrial revolution:
Industry 4.0 is described as a gradual transition from the third industrial revolution to the present and thus builds on electronics, computer technology, and PLCs with an increased focus on digitalization, artificial intelligence (AI), big data, Internet of Things (IoT), and advanced automation. The term is formally marked as first used in the early 2010s. It is about full integration of smart systems that communicate in real-time and enable predictive maintenance, self-governing processes, and hyper-flexible production chains.