Bump test saves lives
New data reveals the connection between bump test intervals and gas detection errors. At Hans Buch, we therefore focus on why it is so important to perform regular bump tests on your gas detectors.
See if your gas detector works with a bump test
There are many reasons why a portable gas detector may not respond to gas – some of which are not visible to the employee wearing the gas detector.
When an instrument is turned on, you can see that the battery and display are working correctly, but what about the internal electronics that play a crucial role in protection? Do the sensors and alarms work as they should, have they been impaired by using the wrong cleaning agents, or are openings blocked by dirt? And how do you find out?
A bump test is the only way to ensure that the entire gas detector is functioning correctly. The test checks that the sensors respond to the gas and verifies that the display also reacts. A bump test also confirms that the alarms are activated and that the detector alarms correctly.
Also read the article: Choose the right gas detector and avoid accidents.
How to perform a bump test?
The purpose of a bump test is to ensure that the gas detector is working optimally by briefly exposing the device to a certain concentration of the specific gas type.
The reading is compared to the actual gas amount as indicated on the test gas cylinder, and if the detector alarms within an acceptable range due to the actual concentration, usually within 10%, it is functioning correctly. If the results are not delivered within an acceptable time frame, or if it takes more than 30-40 seconds to alarm, the gas detector must not be used until a full calibration is performed.
Why don’t people perform bump tests regularly?
The reasons for not performing bump tests are usually always the same:
- It takes too long
- It is too difficult and requires training
- There are no legal requirements dictating bump tests
It takes an average of 20-30 seconds to perform a bump test. Depending on the gas detector used, there are both semi-automated and fully automated systems that can perform the bump test. So the procedure is very simple. The best systems can be configured so that the gas detector only needs to be inserted, and from there the system takes care of the rest – from supplying the gas to measuring the results. Little or no training is required.
The new data, which reveals the connection between bump test intervals and gas detection errors, concludes that gas detectors on which bump tests are performed daily have an average error rate of 0.3%. Compared to gas detectors on which bump tests are only performed every 20 days, a double average error rate is seen. And if we’re being completely honest, what would justify not performing regular bump tests when things really go wrong?
Remember, no matter how often you bump test, it does not replace the need to inspect, calibrate, and service gas detectors regularly by a specialist.
Example: How important is a bump test?
Below we provide an example of what can happen if you do not bump test your equipment. The example is fictional but inspired by real events.
Flemming’s mistake
Flemming works at a local oil refinery and arrives in the morning to perform his daily tasks. He wears all the safety equipment required to ensure his safety. His task that day is to perform a thorough cleaning on site using a high-pressure cleaner.
At the end of his shift, he returns to the locker room to clean up. He cleans his kit using common cleaning agents that contain alcohol and silicone.
The next day, Flemming gathers his equipment and is briefed on his work for the day. Later in the day, while working in a low-lying area, he smells something that smells like rotten eggs, but the smell quickly disappears again, and since his display does not react, he continues to work. Not long after, he suddenly collapses after inhaling high levels of hydrogen sulfide (H2S).
What can we learn from the example?
In this example, Flemming impaired the function of the gas sensor by using the wrong cleaning products – a typical mistake that would have been detected by a bump test.
Sensors can be poisoned or impaired by using the wrong cleaning agents. Alcohol can damage electrochemical sensors, and silicone-based products inactivate catalytic bead sensors, which are intended for measuring LEL gases, such as methane, pentane, and propane.
In both cases, the circuit would still be complete, and the device would give a normal reading. Without further bump testing, Flemming would think it was functioning normally, but the device would not alarm if it encountered high gas levels.
What should Flemming have done differently?
Ideally, Flemming could have avoided this problem by checking which products were suitable for cleaning the detector – possibly hot water in this case. The manual for his gas detector would be a good place to start. The manufacturer also provides additional guidance on how to best clean the device if necessary.
Regardless, Flemming should have performed a bump test when he started his workday. This would not only reveal poisoned or impaired sensors but also any blocked filters or defective sensors. It will also check if the acoustic and visual alarms work. In other words, a bump test would have confirmed that the device alarms when necessary.
Flemming would then have replaced his defective device with a functioning one, and therefore he would have avoided being poisoned by hydrogen sulfide. Fortunately for Flemming, his colleague Lars saw him fall and raised the alarm. Flemming was not seriously injured but had to take two weeks off work to recover.
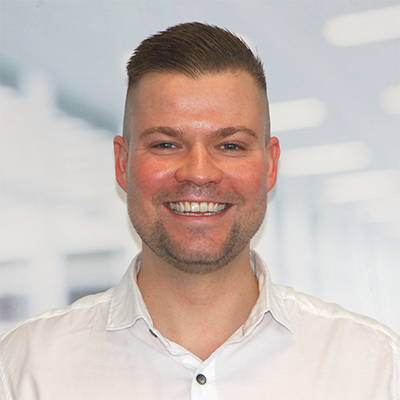