Technical Review: Energy Optimization of MAC Valves
One of the many advantages of our range of valves from MAC Valves is reduced energy consumption, which benefits both the customer’s operating economy and the impact on climate and environment. Here you get a technical review of how MAC valves optimize energy.
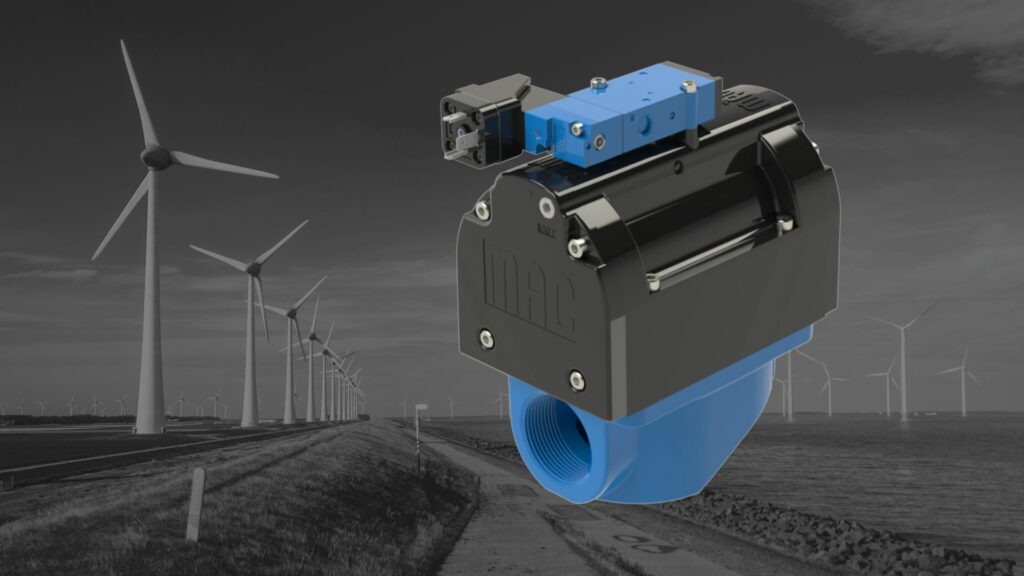
Efficient energy management is a central part of modern industry, and choosing the right components can play a significant role in optimizing operating costs and environmental impact. One of the key players in this optimization is MAC Valves, which Hans Buch distributes.
In this knowledge article, you will gain more technical insight into how MAC’s innovative valve technologies contribute to reduced energy consumption in automated pneumatic systems, and what technical details make it possible.
Traditional valves often have energy waste
Traditional valves often have high energy consumption due to inefficient coil and valve configuration. The coils in these valves require a continuous current to keep the valve open or closed, which can result in significant energy waste over time. Additionally, many traditional valves have a longer activation time, which requires additional energy to maintain the necessary pressure control in the system.
MAC’s technological advantages: How the valves reduce energy consumption
1. Pulse Technology
MAC Valves use pulse technology in their coils, which reduces energy consumption by delivering a short pulse of current to activate the valve and then switching to a low power consumption (holding voltage) to maintain the valve in the desired position. This technique can reduce power consumption by up to 90% compared to traditional valves.
- Activation voltage: 24V DC / 110V AC
- Pulse duration: 5-10 ms
- Holding voltage: < 10% of the nominal activation voltage
- Power consumption during activation: 4-8 W
- Power consumption in holding position: < 0.5 W
2. Internal pressure-balanced technology
Many of MAC’s valves use an internal pressure-balanced construction that requires less energy to overcome the resistance in the system. This further reduces activation time and energy consumption.
- Pressure drop: < 0.1 bar (at 6 bar operating pressure)
- Kv value: High flow capacity with minimal pressure loss
- Response speed: < 10 ms
3. Efficient coil designs
MAC’s patented coils have low inductance, meaning they use less power to generate the necessary magnetic field. This reduces both power consumption and heat generation in the valve’s magnetic system.
- Coil resistance: 80-150 Ω depending on the model
- Maximum heat development: < 20°C above ambient temperature
4. Optimized airflow
MAC Valves use a unique spool and sleeve technology that minimizes friction in the valve’s moving parts. By reducing friction and turbulence internally in the valve, less energy is required to activate and hold the valve in the desired position.
- Lower activation pressure: Can operate at a minimum activation pressure as low as 0.1 bar
- Optimized flow design: Greater flow capacity with lower energy loss
5. Balanced Poppet Design
MAC’s valves are designed with a “Balanced Poppet Design,” which ensures that the pressure force on both sides of the valve is balanced. This reduces the required magnetic force and thus energy consumption.
- Lower required magnetic coil power: Can reduce activation energy by up to 50%
- Faster response times: Under 1 ms in certain configurations
6. Reduction of internal leaks
MAC has minimized leaks through their precise machining and high-precision sealing technologies, which means less energy loss over time.
- Maximum allowed internal leakage: < 0.1 ml/min at 6 bar
- Integrated sealing elements: Use of fluorocarbon and PTFE seals ensures low permeability
7. Pilot control optimization
Many of MAC’s valves are designed as pilot-operated valves, which reduces energy consumption as the smaller pilot valve requires much less energy for activation.
- Less activation force: The pilot valve uses only a fraction of the energy
- Longer lifespan: Fewer energy-intensive shifts lead to less wear
8. Faster response for reduction of air waste
With MAC’s fast response time (often under 5-10 ms), they minimize unnecessary air discharge, which means less energy waste in applications with rapid sequence changes.
- Response time: MAC’s 35 series valves can respond in < 2 ms
- Air waste per cycle: Reduction of up to 30%
Examples of energy savings in practice
A typical industrial application with standard valves can run continuously for 24 hours with a power consumption of 10 W. A comparable MAC valve with pulse technology would use less than 1 W in holding state. For a system with 100 valves, this can result in annual savings of up to 7,884 kWh, equivalent to a financial saving of over 15,000 DKK.
Get ROI calculated with your specific data
At Hans Buch, we not only assist with delivery and installation. As an additional service, we offer to calculate the payback period of your investment in our technical solutions based on your operating data. Contact us to learn more about how we can help provide an overview of your projects when you want to optimize your operations.
Conclusion
Choosing MAC Valves for your automation system can not only reduce energy consumption but also improve the overall performance and lifespan of the system. With advanced technologies such as pulse technology, optimized airflow, and Balanced Poppet Design, MAC valves are an investment that quickly pays for itself through lower energy consumption and reduced maintenance costs.